Automated Aeroponics Garden
Northeastern MIE Capstone, Mechanical Engineer
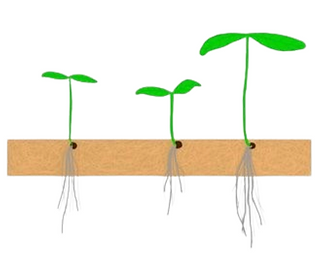
Research
Summer 2023
​
Design & Analysis
Fall 2022
​
V1 Product Presentation
December 2023
​
Location
Boston, MA, USA

Project Motivation
• Urban residents lack space to grow their own fruits and vegetables
• 65% of the earth's freshwater is used for agriculture – 45% of this is wasted
• For produce, 36% of carbon emissions come from transportation
• EPA warns about health risks resulting from pesticide usage

Traditional Raised Bed
• Average raised bed garden size of around 100 sq ft
• Average setup cost of $1800
• Uses 125 gal per week
2 hrs. maintenance per week
Potted Planters
• Apartment friendly
• Less than $30
• Plant type restricted
• Daily watering
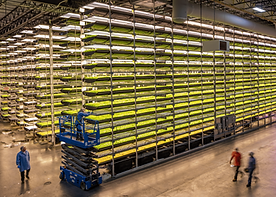
Aerofarms
• Aeroponics
• 69,000 sq. ft warehouse
• Outside of target market
I owned the Climate Controls Sub-System
My "solo" contribution to the development of the product was in the monitoring, and regulation of enviornment conditions. The MVP (minimum viable product) goals of the sub-system were to monitor temperature and humidity, and reach goals included achieve 80+% heating efficiency, and cooling capabilities.
Down-selecting Climate Control System Architecture
​
I used a Pugh Decision Matrix to determine what hardware I should use to monitor, and regulate temperature, and reach for cooling + humidity capability.
​
The results (highlighted/boxed in red showed that the most viable options were:
1. Resistive heating pads, filtered air intake and exhaust
2. Peltier assembly (heating, cooling, dehumidifying), filtered air intake and exhaust
​
Thermo-Electric Cooler/Peltier Module Testing:
Research into TEC's revealed potentially low efficiency for both heating and cooling, but due to the small form factor, limited complexity, and ability to fully control temperature (and humidity), it was worth testing OTS models and vetting it's viability.
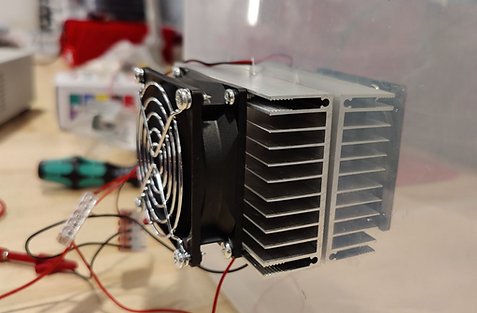

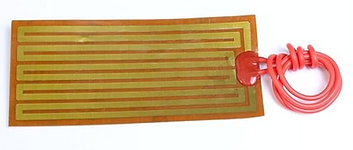

Resistive Heater Final Design:


Heating Prototype Comparison
Lighting Sub-System:
Provides the proper amount of light to the plants for optimal plant growth. Custom Light PCBs developed to decrease cost, while maintaining the same performance metrics as OTS lighting solutions such as PPFD (Photosynthetic Photon Flux Density), power consumption, etc. These were designed from scratch and we had them produced by an oversea manufacturer.
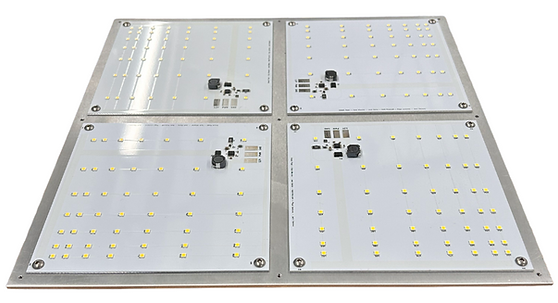
4 Light PCBs on mounting plate

Visualization of "FOV" of each diode on Light PCB
Key Information
• Even/consistent distribution of photons across the plant growth plant platform dude to the geometric distribution of diodes
• ~5x cheaper/plant growth enclosure compared to OTS lighting
• ~6x smaller overall height compared to OTS lighting
• Limited need for active convection cooling
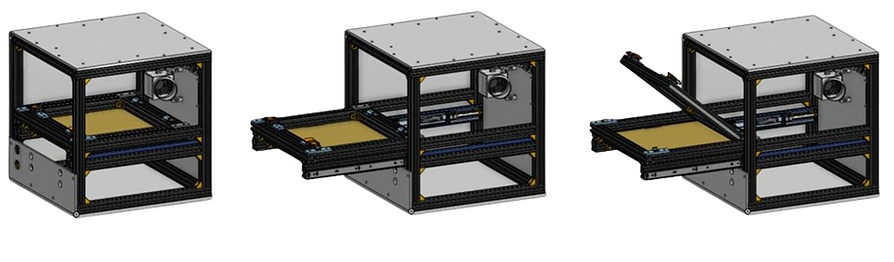
Stages of Plant Platform Motion/Loading Sequence

Sealed Fluid Delivery Connections

Pump System Schematic

Sub-System in Module
Key Information
• Arduino Nano control
• Solenoid valves, pump, relays, fans, heating module all supported
• Sealed connections
• Temperature monitoring and control
Final Design
Our final design was successfully able to support 2x efficient plant growth compared to conventional methods by regulating temperature, nutrient and water delivery, light cycles in a way that is optimized for each species while being resource efficient. It can run autonomously for 4 weeks without intervention, support up to 7 plant growth modules, and gives the user easy access to planting and harvesting.
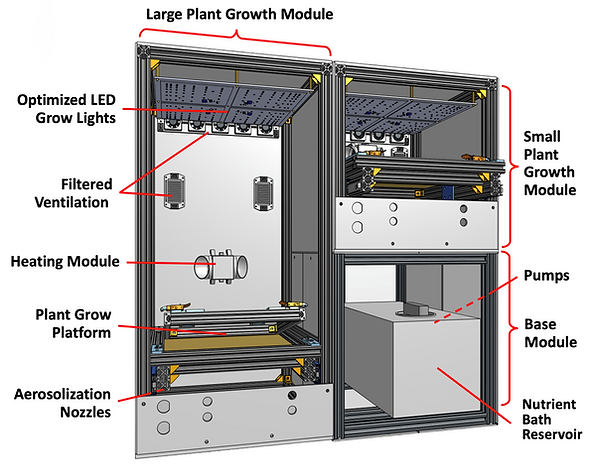
Component Level Diagram
Photo of plants being supported on Coco Coir plant growth substrate

Research:
My team and I spent the summer researching what helps plants to grow, existing methodologies for optimized plant growth, conducting market research and establishing a plan for the coming fall where we would then execute on our design/analysis plans. During this phase of the project, we formalized our problem statement, our goals, and created a Gantt Chart to map out our plan.
.jpeg)
Problem Statement
To design and validate a system to bring personalized agriculture to consumers – the ability to grow fresh, pesticide-free produce in their home efficiently, while minimizing cost and improving accessibility.
Target Market
• Apartment dwellers
• 50% of an urban residents report interest in renting agricultural plots
• Homeowners
• Convenient access to affordable, fresh produce.
• Environmentalists
• Increased space-efficiency
• Reduced waste and transportation emissions
Comparing Plant Growth Methods

Hydroponics
• 85% less water use
• 3-30 times more space efficient
• 200% faster growth
• Cost $60 to $1000 for consumer models
• Cannot grow certain plants
Aeroponics
• 98% less water use
• 3-30 times more space efficient
• 450% faster growth
• No consumer product options
• Higher complexity
• Cannot grow certain plants
State of Aeroponics and Hydroponics In Industry

Aerogarden Bounty Elite
• Hydroponics
• $999
• No controlled environment

Gardyn 3.0
• Hydroponics
• $334
• No controlled environment
Design, Analysis, and Testing
Throughout the fall, my team and I utilized software including OnShape, ANSYS, MATLAB, Microsoft Excel, fabrication methods including soldering, 3D-printing (Prusa, Stratasys), power/hand tools, laser cutting, CNC milling, and engineering design tools including tolerance stack-ups, Pugh decision matrices, hand calculations, etc. to deliver a strong V1 design for an industry first automated garden system which leverages aeroponic technology in the consumer product space.

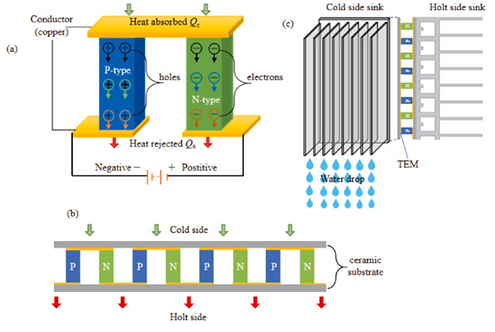
Heating
• Efficiency: 68.5%
• Minimum Enclosure Temp: 73.5ºF
• ∆T: 10ºF
Cooling
• Efficiency: 9.3%
• Minimum Enclosure Temp: 73.5ºF
• ∆T: 3.7ºF
Results
The TEC/Peltier module did not have viable cooling efficiency, and required far too much power draw for heating. This strategy for climate control was tabled, while other options were explored.
​
Improvements that could be made:
- Custom heatsinks
- Improved heatsink contact

Resistive Heater Initial Testing:
After the lack of efficiency and cooling capabilities of the TEC module, I turned my efforts to resistive heaters after conducting research into their efficiency, form factors and industry applications. In the event that results showed high efficiency, a custom module could be constructed to improve performance in out V1 product.
Test Setup
An aluminum plate was fitted with many resistive heaters, 8 x 7W heating pads, in an enclosure with no insulation that is similar in volume to the plant growth module in our teams expected V1 product.
Results
This heating method seemed very viable.
Improvements that could be made:
- Increased velocity over heaters
- Custom ducting
- Better heating pad mounting
Heating
• Efficiency: 65%
• Max Module Temp: 96ºF
• Max Module ∆T: 87ºF

Graph used to calculate efficiencies



Performance
• 35W Resistive Heater
• 25 CFM Fan
​
• Efficiency: 82.4%
• Max Module Temp: 96ºF
• Max Module ∆T: 21ºF
Heating Module Design
• 3D printed
• Heatset inserts
• Hole and slot alignment features
• Integrated cable management features
Air Intake/Exhaust Design
• 3D printed
• OTS fans
• Snap fit filter installation features


Testing Light PCBs
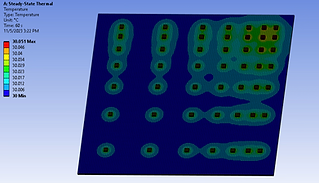
Thermal Sim on Light PCB
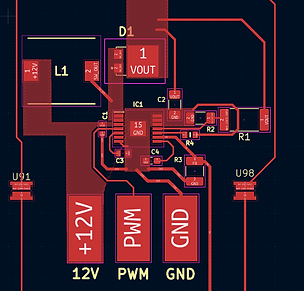
Highlight of Light PCB Schematic

Drawing of Plant growth in Coco-coir substrate

Key Information
• Quick release/sealing plumbing connections
• sealants and caulk used to fill gaps and seal complex geometries
• Bubble gaskets used on hinging door for reliable repeated sealing
Sealed Electronic Connections

Key Information
• 2 misting nozzles per module
• 7 modules supported
• Arduino controlled pump duty cycles
• 5 gallon reservoir (4 weeks sustained use before refill (1 module)).
Graph of Pressure Drop vs # of Modules
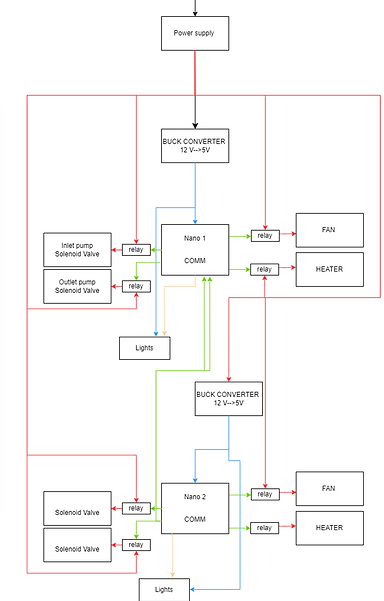
Electrical/Control System Schematic

Photo of V1 Prototype on Capstone Presentation Day
.jpeg)

Photo of plants roots growing through Coco Coir plant growth substrate

Render of V2 Product, designed for easily fabrication, manufacturing, and "product" form factor
Other Sub-System Highlights
Below I have summarized the details of each of the other sub-systems. I played an important role in the planning, project management, and supported the technical development efforts of each of these sub-systems, although I did not perform all of the detailed design and analysis work for each of the sub-system such as the PCB design.

Caulk and Sealing Material Testing
Structure/Sealing/Plant Platform Sub-System:
Allows the user to easily prep for plant growth and harvest grown plants using a sliding drawer system, which is familiar to consumers, and utilizes a "t-shirt press" hinging mechanism to secure the plant growth medium, coco coir (a coconut husk sheet material that allows the plant to be supported and expose their roots to the air. This sub-system also dealt with sealing the structure, and supporting all of the other subsystems in a compact form factor.
Plumbing/Nutrient Delivery Sub-System:
This sub-system delivers water and nutrients in mist form to each of the plant growth modules. The goal was to have a pump system that could support multiple modules without swapping components such as tubing, electronic controls, pumps, etc. so we performed calculations for pressure requirements to support multiple modules. Ultimately, our V1 product can support 7 plant growth chambers without swapping hardware.
Power/Controls Sub-System:
This sub-system interacted directly with all other sub-system, as it regulated all electronic control for the product. Arduino Nano's were used to traffic information and power, and relays and buck converters, helped manage various voltages/current required for safe operation.
Next Steps:
Continue developing this to a V2 product stage with funding secured through prototype/startup funds on campus, currently endowed with $1500, with $3000 more expected in the coming months (written Jan 2024).