FSAE Chassis Research and Development
Northeastern Electric Racing, Technical Lead + PM

Research and Design
August 2022 - January 2023
​
Fabrication
Spring/Summer 2022
​
Location
Boston, MA, USA

-22% Weight ✓
Incorporated Side-Pods ✓


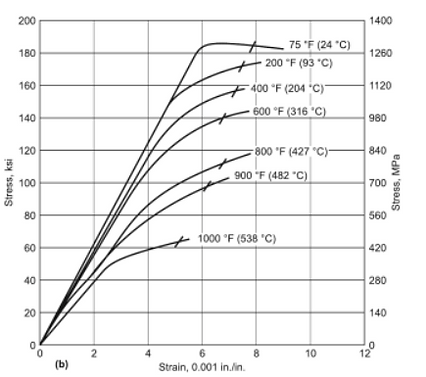





Front Torsional

Side Impact
Research (Structural Concepts, Rules, etc.):
This was the first stage of the project's progression towards completion. I began extensive research into FSAE (Formula Society of Automotive Engineers) rules databases, as this as the clubs first time competing this higher level environment. There were more frequently updated rules, inspections, etc. In addition to these rules, I had to become very familiar with terminology to effectively lead the team. My design intuition for this subject matter began to mature through this research phase.
Project Management:
This was arguably the most challenging part of the project. I was responsible for the longest work package in the club, and the first design project of the newest (and first totally new) car since the clubs conception.
​
I aimed to split the streams of input into 4 paths, drivetrain, handling, tractive and ergonomics. These 4 main systems would have the highest impact on the major dimensions of the chassis. This proved helpful as I was able to open consistent dialogue with the leads and heads of those groups rather than speaking to every lead in bulk or any other variation that would require more effort than it was worth. (ex. low voltage proved to only need bi monthly catch ups, so I essentially put them on the back burner expect when major revisions came up)
Extensive Design Period:
I led the design process through about 4 major design revisions, with 9 semi-major revisions. We experimented with bent members to reduce total part count and improve ease of jigging or manufacturability. We used FEA to determine structural integrity of joints and if the minimum wall thicknesses we applied to the CAD model were sufficient to maintain the factor of safety (FOS) that we wanted. I would consider all recommendations and have new members take on the responsibility of trying out said idea, interacting with my models via SolidWorks PDM and using Slack to send pictures of key measurements to provide edits/thoughts throughout the school week.
Concept of Designs:
Starting with hand sketches, whiteboard drawings and pointing our fingers together to mimic joints of the chassis was where the design process started. In addition to looking into other teams chassis that is, haha. At a certain point during the concept of design stage, I had to take a step back and ask myself what were the major components of the chassis, why are they considered major and are there potentially multiple use cases for chassis members aside from the obvious. Lightweight designs came out of this stage, most of which needed to be built out more due to rules compliance.
​
The biggest accomplishment during this stage of the project was picking 4130 Chromoly steel for the NER22A Chassis. Coming from 1010/1040 steel backgrounds. This would be a major improvement. The density was the same the latter 2 steel types, but it had much more attractive specs, including yield strengths and young's modulus etc. These better properties allowed the minimum wall thicknesses to be applied to the chassis design, whereas the existing chassis had thick tube walls which increased weight. The trade off was cost, yet due to club financials, management agreed this was not overly expensive.
Applied Mechanical Design Skills, Improved Management Practices, Provided leadership
Final Design:
This is the final design of the chassis that was presented to the team and pushed to fabrication in early 2023. FEA was performed, simulating front impact, side impact, roll over, front torsional and rear torsional events using forces calculated and paired with published parameters and vehicle behaviors in FSAE rules, documentation, etc.
​
The design features side-pods which tend to increase weight, which is a sacrifice for vehicle dimensions. Despite this, the chassis featured a drop of 22lbs overall and if side-pods are omitted from the comparison, the chassis was reduced by approximately 40lbs! This was a huge accomplishment for the team as this was the second chassis produced by NER.
​
The design was done with the team in mind. This chassis was designed with the team in mind, and constant communication was used to make the car more easily maintainable and troubleshoot during testing. I feel that this will save time and energy for the team worth so much more than the extra pound that was added in doing so. :)
