FPV Cinematography Drone Build
(First-Person-View)
Personal Engineering/Cinematography Project
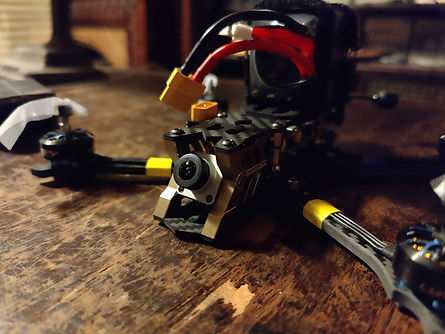
I built a First-Person-View Racing Drone with both off the shelf electronic components as well as personally fabricated parts, while utilizing, research project organization skills (Excel, Visio, etc.), mechanical assembly (hand tools, soldering, board wiring, and stress testing) and CAD (SolidWorks).
​
I expanded on my workplace developed skillset in PID tuning, thrust analysis, and power optimization to surpass my goals for 5 minute flight time, stability control and <25ms video transmission delay.
​
Using force analysis practices, and part specifications I was able to choose the most optimal carbon fiber frame available and correct for my use case.
​
This was a very interesting project that linked my education with my work experience and personal interests! I hope you think so too!
​
Below I have expanded upon my research and design process with descriptions of each stage and media to go along with it.
Project Timeline

Late Autumn 2021
Project "Spark"
Decemeber 2021
Research
New Year 2022
Planning/Sourcing
Spring 2022
Fabrication and Assembly
Spring 2022
Flight Training (FPV Simulator)
Spring 2022
Verification, Test Flights and Troubleshooting
Cruising and Filming
While fighting my way through my mechanical engineering courses (Thermodynamics, Electricity and Magnetism, Mechanics and Materials, etc.) I watch hours of YouTube videos of FPV pilots doing impressive diving maneuvers and flying through tight spaces. This was a movement style my current done setups were not capable off, and I knew I had to build a drone from the ground up to achieve these cinematic effects.
What is an ESC? What is a brushless motor KV rating? How do I know which leads to solder to the PDB? What does a flight controller actually do?
----
These were all questions I researched in order to understand this build from an engineering perspective. I could follow a tutorial like a robot, but this project is about challenging myself and learning, in addition to seeing the world from the POV of a falcon.
I began this portion of development by researching products in the consumer market that would be fit my design requirements and budget. These parts included, carbon fiber frames, lightweight ESC's, Flight controllers, power management hardware, motors, fixture hardware and (what brought the most challenge) radio + digital signal hybrid communication hardware. Here I was faced with a fork in the road, expensive vs cheap build... I choose expensive, here is why.
​
DJI, a drone manufacturing giant has produced a highly digital FPV system that uses Phased-Array Radar and high bandwidth digital communication lines to achieve HD quality live stream to their heads up display googles without losing the low latency video feed that FPV pilots desperately need. This system can be incorporated in my custom build, but not at a low cost. While working at MatrixSpace, Inc. an autonomous UAV/Sensor fusion start up in Burlington, MA as a mechanical engineering coop, I was exposed to advanced RF technologies, and digital data links to provide strong remote connectivity. This working experience pushed me to build a higher end product rather than something that worked but had avoidable downsides (video quality mainly).
​
CHASSIS: After speccing the motors from a weight estimate and flight time goals, I knew that I needed a frame with specific requirements. Doing simple calculations and CAD modeling, I was able to then purchase the cheapest frame that would support my flying style, and forces experienced in the frame. Additionally, I anticipated that a few modifications needed to be made as no drone chassis was able to satisfy goal I set, so choosing the correct frame (one that could be broken down slightly, but still maintain structural support) was even more crucial.
As parts were delivered, I began to build the aircraft. Starting with the frame, I used electronics repair hand tools, calipers and X-Acto knives to assemble the carbon fiber frame. I then mounted the Electronic Speed Controller (ESC) and Flight Controller (FC) Stack onto the center of the frame, and did the same for each of the 4 brushless DC motors (2250KV).
​
Why 2250kV Motors? Why These motors specifically? I choose this KV rating after studying this motor metric/specification at my job at the time, Mechanical Engineering Coop at MatrixSpace, Inc. while doing a deep dive into thrust shortage solutions for a future generation of UAV's. 2250kV in a 6S LIPO battery powered drones would produce a theoretical (minus air resistance from the propellers) 49,950 RPM. high rpm with small propellers (lower surface area), which are great for FPV maneuvers. These motors were recommended by FPV professionals... and were on sale, haha. the thicker wires carry more current and therefore can yield higher RPM. This should let me recover from flight errors and perform aerial acrobatics extremely fast, and more importantly, carry a second cinematic camera!
​
Another challenge was soldering the ESC and Flight Controller to the motors and transmitter/receiver module. I applied my soldering skills to attach 12 leads to the speed controller and a few smaller leads onto the flight controller.
​
I utilized CAD (SolidWorks) and additive manufacturing (3D Printing) to create some parts for the setup (wire management, antenna routing, etc.)
Training in a flight simulator is a crucial part of this hobby. It allows pilots to improve their handling skills and use of the their custom controller configurations. Furthermore, I was able to input my own drones' parameters (PID controller tunes, weight and size) to better practice controller MY UAV.
This was the most frustrating part of the project because everything that I learned online and at work wasn't enough to avoid problems. Motors becoming twitchy during flight required better solders and routing, and software was a whole seperate battle. I tried to be resourceful and ended up reaching out to a club of hobbyist drone pilots and engineers at Northeastern University to gather tips and software "hacks" to assist in troubleshooting. Problems still arise to this day but "thats FPV" as they say, despite good engineering practices and care, haha.
Enjoying my project! Hopefully this is something stick with for years to come! Thanks.

Design Requirements/Goals
1. 5+ minute flight time (a lot for FPV)
2. No component interference with GoPro FOV
3. Stream HD video to FPV goggles at low latency (<30 ms delay)
4. Support up to 6S (6 cell) LIPO Battery
5. Reduce EMI (Electromagnetic Interference)
-----
6. Look really cool!
​
Specifications Summary
Motors: 2250kV rating brushless
Electronic Speed Controller/FC: F45A 3-6S BLHeli_32 4-in-1 ESC, T-Motor Mini F7
Chassis: Modified carbon fiber frame, lightweight metal and nylon bolts
----
Communication and Video Module: DJI Air Unit
Controller: DJI Remote (mode 2)
FPV Goggles: DJI FPV Goggles 2
​
​